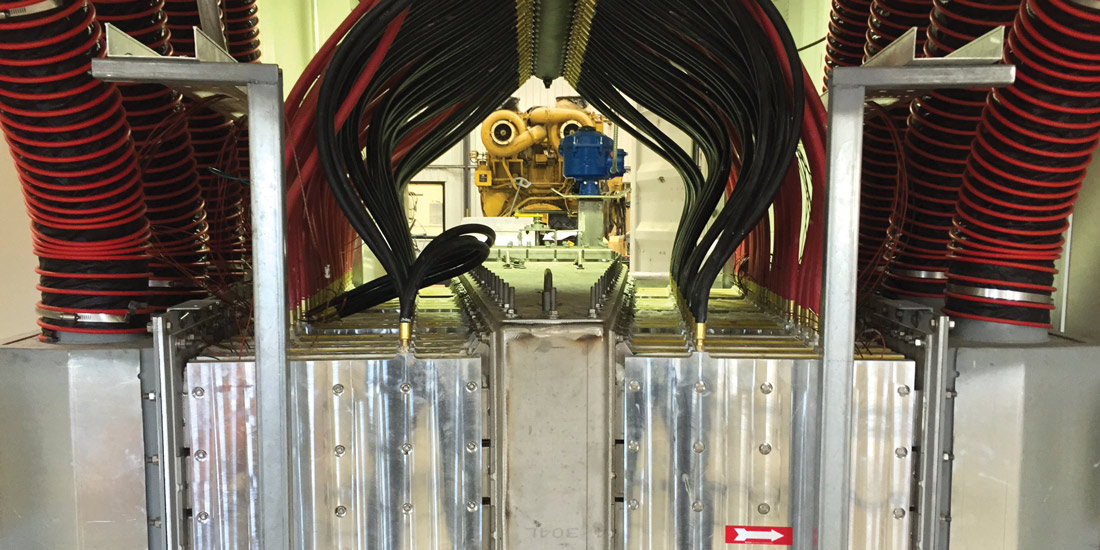
Thermoelectrics: An old, new tech
A sprawling business park, near a patchwork of former salt ponds on the Hayward shoreline, houses more than its share of biotech and energy startups bent on changing the world. Tucked inside these nondescript boxes are companies making innovative batteries to store power from solar and wind farms, ingestible sensors called smart pills to help patients monitor medication intake and, at the offices of Berkeley-born Alphabet Energy, devices to convert wasted exhaust heat into clean, renewable power.
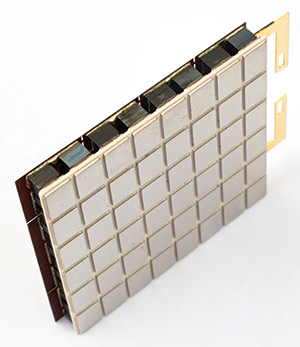
The PowerCard is Alphabet’s most basic thermoelectric device for turning waste heat into electricity.
As physicist Thomas Seebeck discovered in 1821, certain materials that efficiently conduct electricity but not heat can transform any temperature differential into voltage by exploiting the flow of electrons from a warmer area to a cooler one. Engineers, inventors and entrepreneurs have tried to capitalize on the phenomenon ever since, using thermoelectrics to power radios, refrigerators, pacemakers and spacecraft. Others have attempted to turn waste heat from engines and industrial sources into electricity on a larger scale, but with limited success due to the low efficiency and high cost of thermoelectric devices.
Until now, that is. Seven-year-old Alphabet Energy is producing the most efficient thermoelectric devices ever made for waste-heat recovery, using abundant, cheap and scalable materials. CEO Matt Scullin, who founded Alphabet as a materials science graduate student at Berkeley in 2009, is working toward creating and cornering a new thermoelectrics industry by harnessing a vast resource: combustion exhaust heat from cars, trucks and power plants.
To illustrate the potential size of the thermoelectrics market, Scullin offers a back-of-the-napkin calculation. On average, two-thirds of all energy produced is lost as heat. With global annual energy consumption around 104,000 terawatt hours (about 33 percent of the total energy produced), it follows that 208,000 terawatt-hours are lost as heat in the process. If thermoelectrics could recover a conservative 5 percent of that, at the going rate of 10 cents per kilowatt-hour, that’s a waste stream theoretically worth $1 trillion per year.
“Waste heat is everywhere,” Scullin says. “It is an absolutely huge opportunity.”
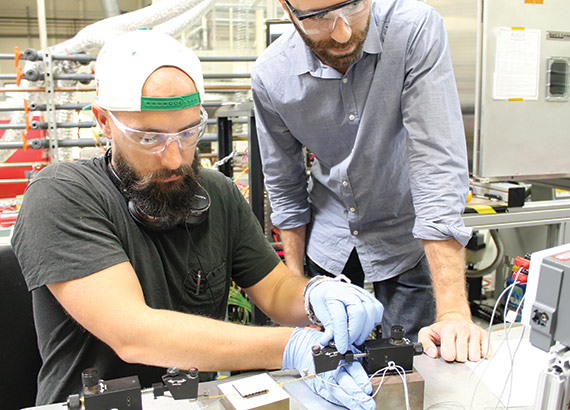
Alphabet Energy CEO Matt Scullin and engineer Jordan Chase measure the PowerCard’s properties in the company’s Hayward lab.
But there’s a greater good behind it all, too. By improving the efficiency of generators and engines while potentially displacing large amounts of energy produced by carbon-emitting sources, Alphabet’s technology could be a boon for climate-change mitigation. According to estimates using government data by the industry group Heat Is Power (where Scullin is on the board of directors), waste-heat recovery at existing U.S. oil, gas and manufacturing plants alone could save enough energy to power 11.4 million homes a year.
Scullin first started thinking about waste heat and thermoelectrics in 2005, while pursuing his Ph.D. dissertation under co-adviser Arun Majumdar, then a professor of mechanical engineering at Berkeley. “He kind of turned me on to the idea of waste-heat recovery,” Scullin says of Majumdar. “Waste heat to me from the get-go was really, really interesting just because of the sheer size of the opportunity. I recognized that if we could just take a small fraction of this waste heat it could make a huge impact, but I was confused as to why this wasn’t being done already.”
Scullin found that existing approaches to large-scale waste-heat recovery were too complex and too costly. The solution, he came to believe, lies in simpler thermoelectric devices, particularly if they could be designed around cheap, abundant materials. Through a larger Department of Energy (DOE)-funded effort at Berkeley to develop thermoelectric generators for use in vehicles, he began studying a class of materials known as complex oxides — but eventually encountered an even better idea: using silicon nanowires to potentially quadruple the efficiency of other known thermoelectrics.
Scullin completed his dissertation, then promptly scuttled the technology he’d been studying in favor of taking a silicon nanowire product to market. “I love to tinker, I love to mess around with things,” Scullin says in retrospect. “It’s probably one of the main reasons I founded Alphabet.”
Majumdar, who went on to direct the Advanced Research Projects Agency at the DOE and currently teaches at Stanford, says Scullin’s timing was perfect. “When we actually discovered that silicon was great and showed all these amazing properties, he was on a parallel project. He was watching all that happen.”
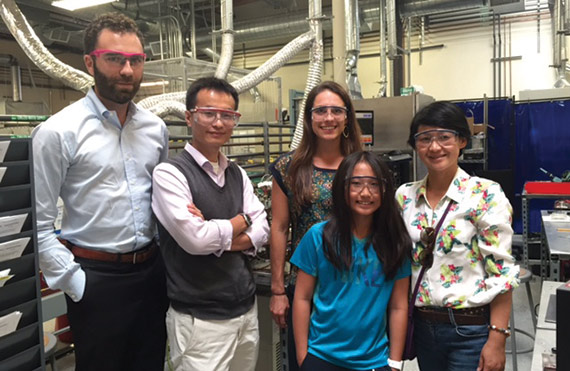
Co-founder, scientific advisor and MacArthur Fellow Peidong Yang on a plant tour with his family, Scullin and engineer Lindsay Miller (Ph.D.’12 ME).
Scullin co-founded Alphabet in 2009 with Peidong Yang, materials science and chemistry professor and faculty scientist at Berkeley Lab — and a partner in the DOE thermoelectrics project — after the pair licensed a patent from Berkeley Lab and the university’s intellectual property office. Yang, whose research group led the development of the silicon nanowire technology starting around 2002, was named a MacArthur Fellow last fall for his work with semiconductor nanowires and nanowire photonics. He currently sits on Alphabet’s scientific advisory board.
In 2014, with silicon nanowire technology still in development, Scullin and Alphabet licensed another promising new thermoelectric, this time from Michigan State University. Based on an affordable and readily available mineral called tetrahedrite, it offered impressive efficiency: not as good as silicon nanowires but still better than anything else available.
Within a year, Alphabet had shipped its first products.
The PowerCard, which resembles a tortilla chip-size solar panel, is Alphabet’s most basic thermoelectric device for turning waste heat into electricity. As with all Alphabet technology, its preferred heat source is vehicle and generator exhaust at 300 to 600 degrees Celsius (572 to 1112 degrees Fahrenheit). A single PowerCard made with tetrahedrite can generate up to 9.2 watts of power simply by being exposed to pressurized hot air: no moving parts or emissions required.
The tiny cards can be sold individually, but they’re also at the heart of Alphabet’s fully enclosed, drop-in thermoelectric generator. The PowerModule, which measures 20 inches long, 24 inches wide and three inches thick — about the size of an extra-large pizza box — contains from a few dozen to more than 100 PowerCards, depending on whether the modules are destined for industrial use in generators or for vehicle use.
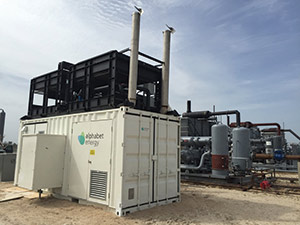
Alphabet’s products are modular and work across scale to capture waste heat to convert to electricity. The E1 system is packed inside a standard ocean freight-sized container and designed for heavy manufacturing and industry.
Commercial application in vehicles is the holy grail for thermoelectrics, Scullin says. The PowerModule can be inserted directly into a vehicle’s exhaust system: hot air goes in one end and out the other, just as with a muffler or catalytic converter, while it silently converts the energy in the waste heat into usable electricity, which is in turn fed back into the vehicle, offering a mileage improvement of up to 5 percent.
Another challenge is navigating the auto industry itself, which isn’t exactly known for turning on a dime. But the company has already made inroads by teaming with a U.S. manufacturer of exhaust systems to explore automotive applications, and last year it signed the first-ever commercial deal for thermoelectric waste-heat recovery with a global automobile manufacturer, which has yet to officially announce the deal. Scullin is hopeful that the PowerModule could find its way into production vehicles “relatively quickly.”
The task ahead for Alphabet comes down to the bottom line, says Majumdar. “The technology has to be at a scale where it can produce electricity at a lower cost than the retail cost of electricity. If someone can do that in a cost-effective way, it’s a big deal.”
Scullin believes Alphabet’s thermoelectrics already offer an attractive return on investment in both industrial and automotive applications. “The economics of this can be very, very good to the customer. They are already as good as solar, and we see how much solar has been adopted,” he says. “Waste heat is one of the greatest untapped resources that we have.”
Thermoelectrics history timeline (from Alphabet Energy):